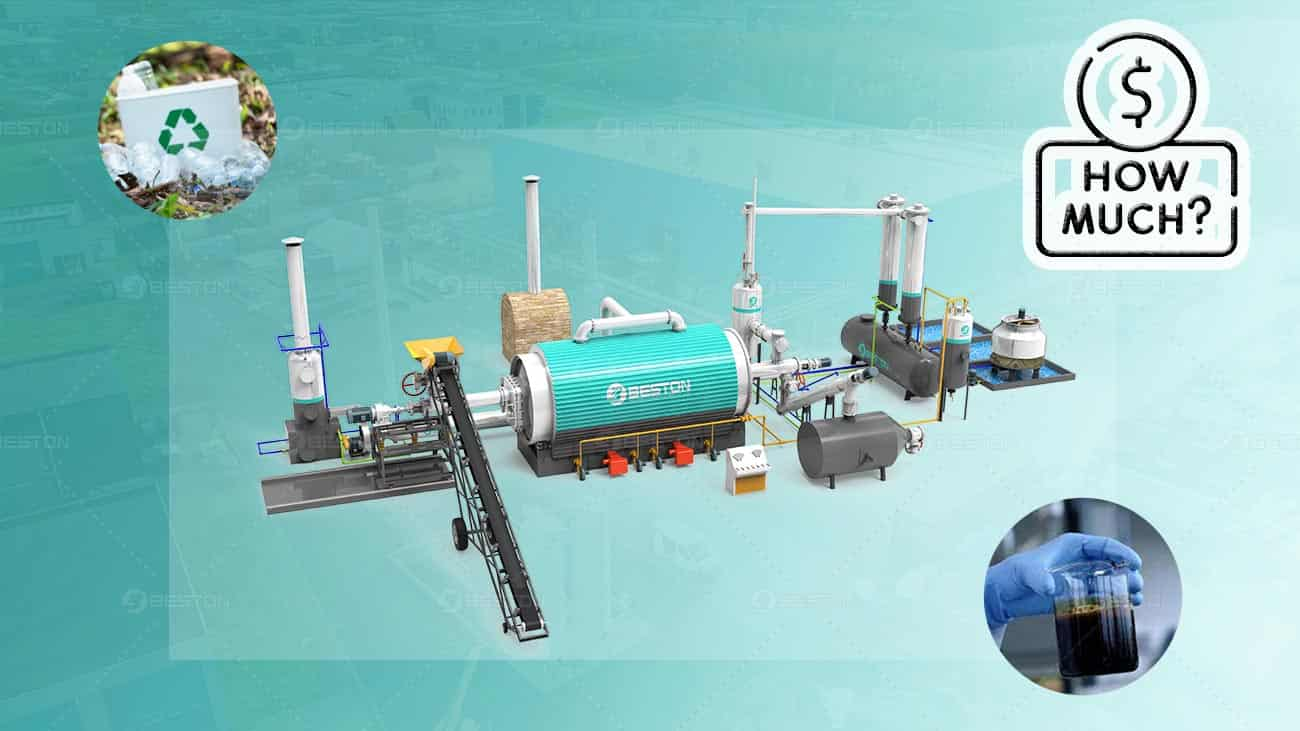
How Configuration Influences Pyrolysis Plant Price
How customization configurations of pyrolysis plants impact prices. Explore aspects from production capacity, environmental and safety features.
© 2024 Crivva - Business Promotion. All rights reserved.