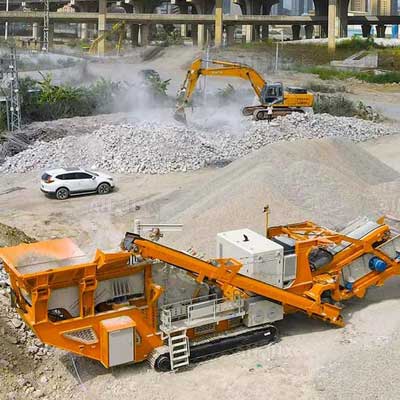
How to Achieve Mobility in Mobile Crushing Plant
Discover how autonomous mobility transforms mobile crushing plants, enhancing efficiency, safety, and sustainability in mining operations.
© 2024 Crivva - Business Promotion. All rights reserved.