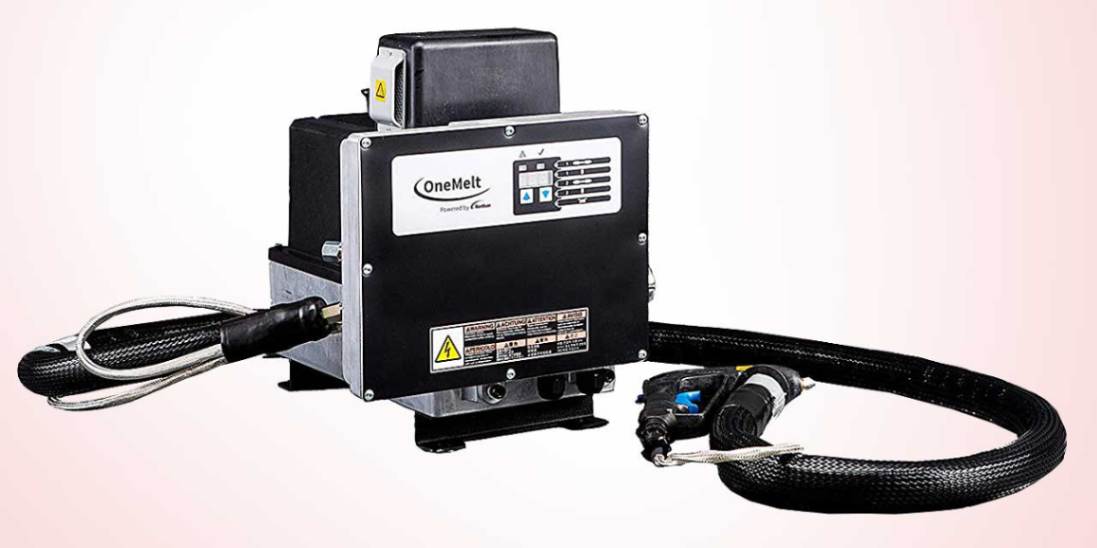
Hot Melt Dispensing Systems
Hot melt dispensing systems are essential tools used in various industries, especially in packaging, manufacturing, and assembly processes.
© 2024 Crivva - Business Promotion. All rights reserved.