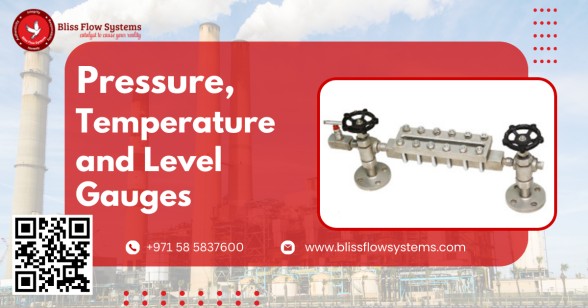
Pressure vacuum relief valve and its primary function
Pressure vacuum relief valve is designed to protect your tank from damage created by overpressure or excessive vacuum.
© 2024 Crivva - Business Promotion. All rights reserved.