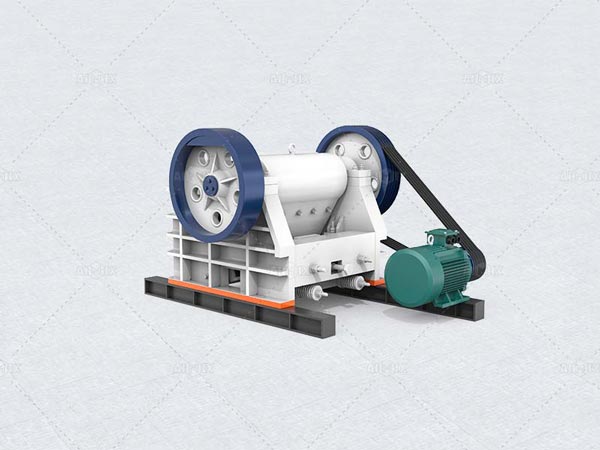
Top 5 Jaw Crusher Brands: A Comprehensive Comparison
Compare the top 5 jaw crusher brands, including AIMIX, for efficiency, durability, and innovative design features.
© 2024 Crivva - Business Promotion. All rights reserved.