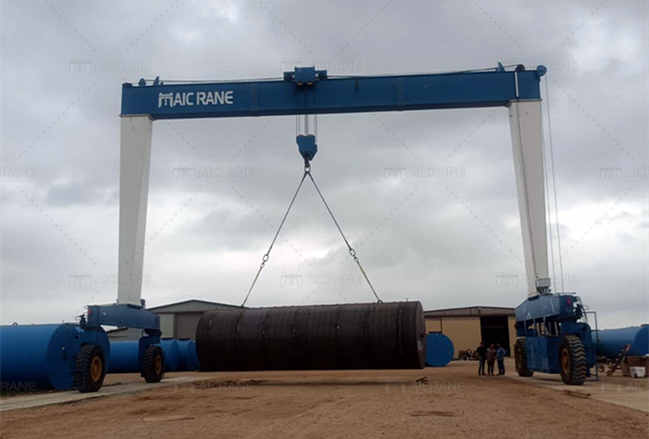
Tips for Choosing a Double Girder Gantry Crane for Sale
Investing in a double girder gantry crane for sale is a significant decision for businesses that require heavy lifting solutions.
© 2024 Crivva - Business Promotion. All rights reserved.