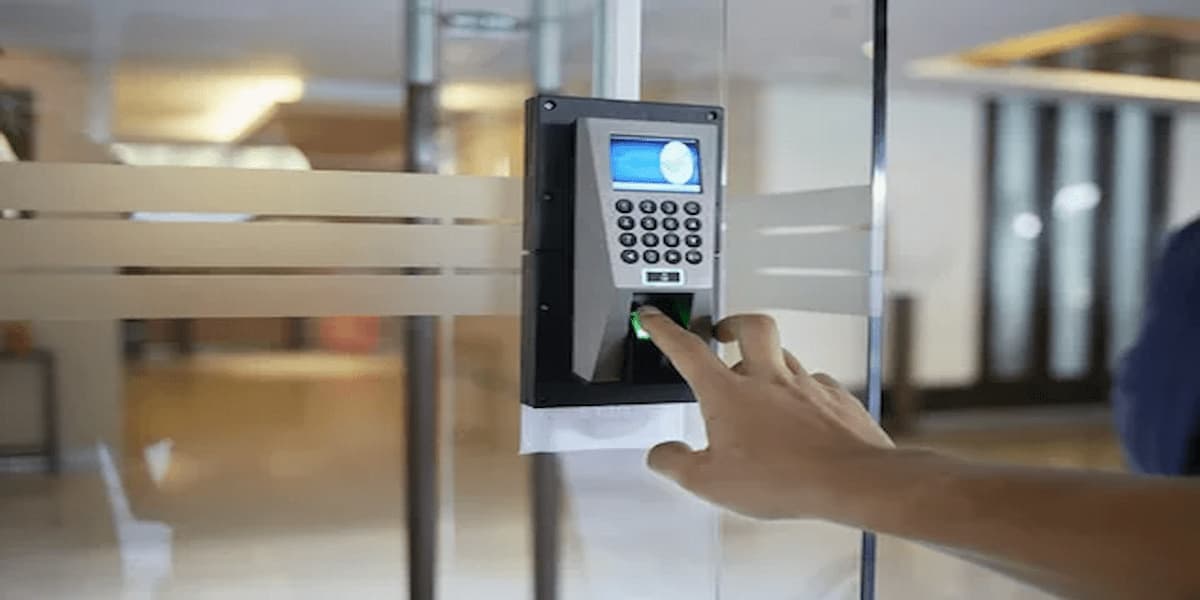
What Will Be The Evolution of Access Control Systems
Exploring future trends shaping the evolution of smart and secure access control systems.
© 2024 Crivva - Business Promotion. All rights reserved.