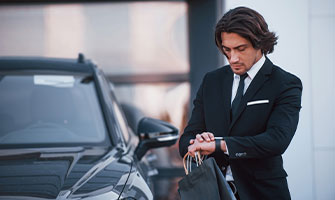
Limo Service Lincoln Chauffu
Book your next ride with Chauffu and experience the difference of quality transportation at an affordable price.
© 2024 Crivva - Business Promotion. All rights reserved.