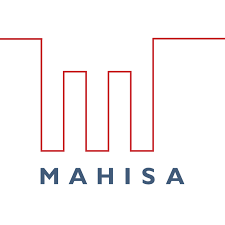
Mahisa Manual Glue Dispenser for Precise Packaging
Discover how Mahisa’s manual glue dispenser offers precision, ease, and efficiency for modern packaging needs with a compact and user-friendly design.
© 2024 Crivva - Business Promotion. All rights reserved.