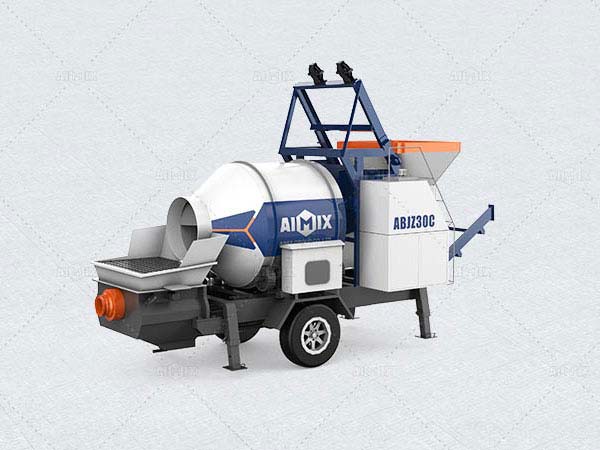
Ways To Keep Concrete Pumping Costs Down
Here are some ways to guide you on how to reduce the concrete pumping cost. Learn more now.
© 2024 Crivva - Business Promotion. All rights reserved.