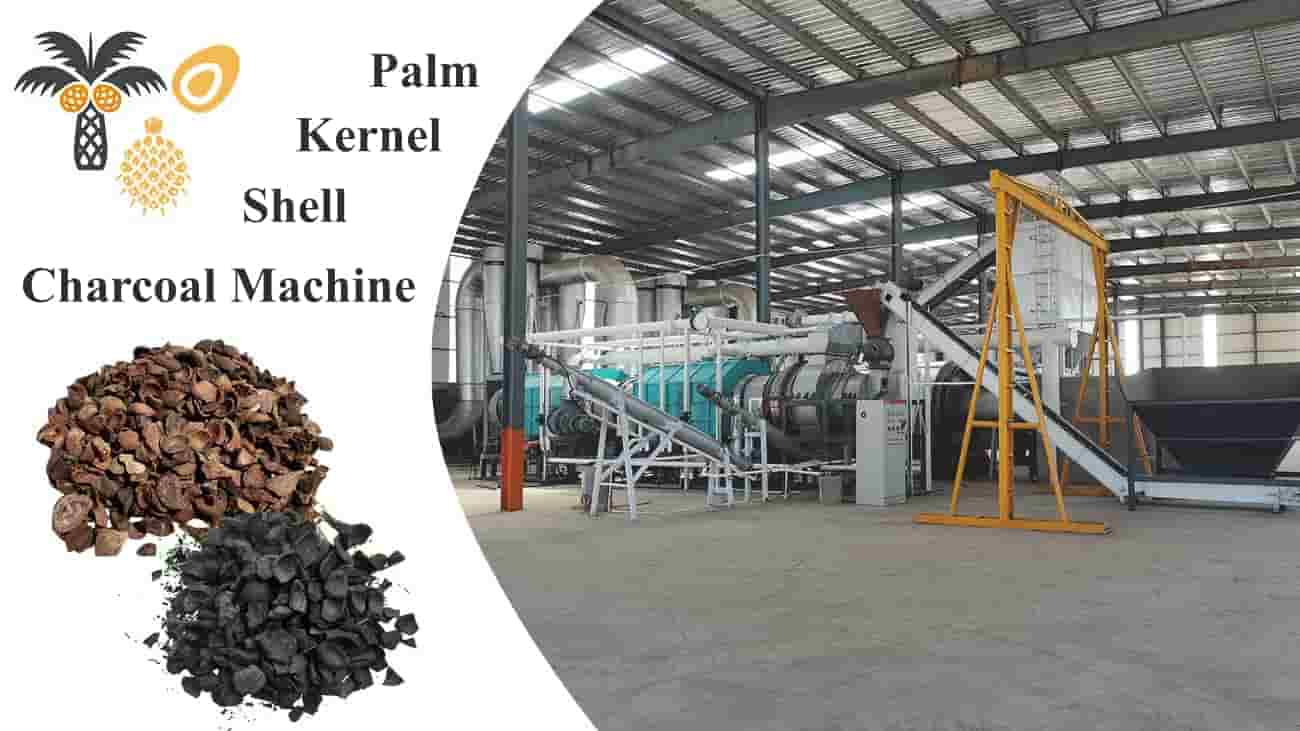
Zero-Waste Approach in the Palm Oil Supply Chain
With the right biochar pyrolysis technology and mindset, palm oil production can evolve into a zero-waste system.
© 2024 Crivva - Business Promotion. All rights reserved.