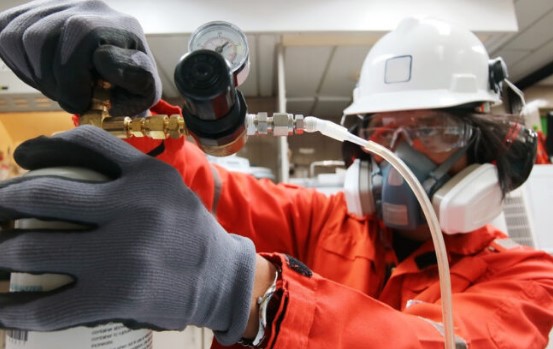
How Often Should You Do Gas Detector Calibration
Learn how often you should do gas detector calibration in Singapore. Keep your workplace safe with expert calibration services and compliance guidelines.
© 2024 Crivva - Business Promotion. All rights reserved.