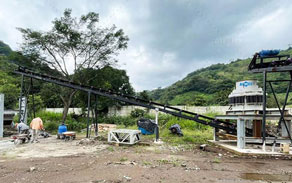
100 TPH Stone Crusher ROI: How Long Pays for Itself
Discover how quickly a 100 TPH stone crusher pays off and boosts your quarry business profits effectively.
© 2024 Crivva - Business Promotion. All rights reserved.