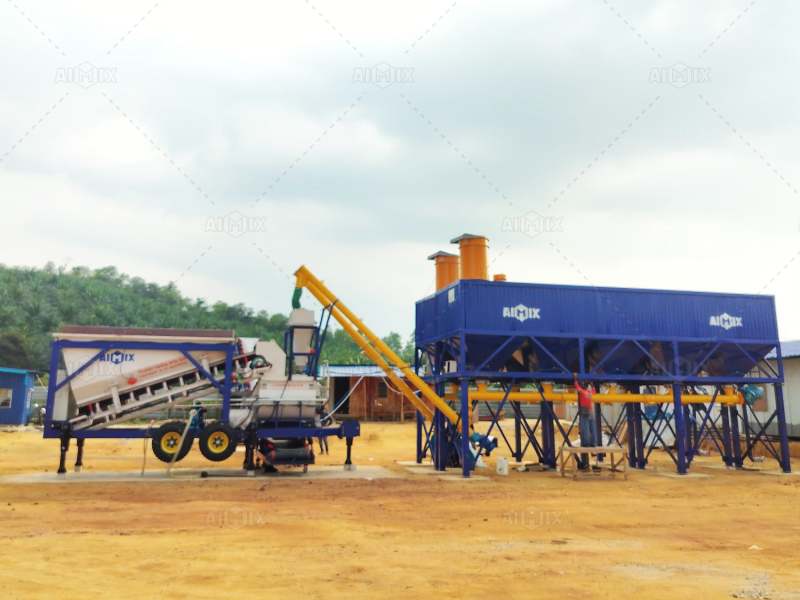
Growth Opportunities for Small Concrete Batch Plant
Small concrete batch plants offer affordable, flexible solutions for growing global construction demand.
© 2024 Crivva - Business Promotion. All rights reserved.