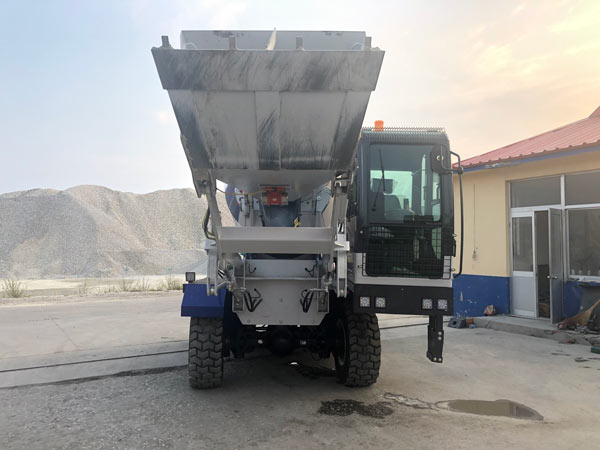
Smart Features in Modern Portable Concrete Mixer
Portable concrete mixer helps save time, materials, and effort. Builders can finish projects more easily with these smart tools.
© 2024 Crivva - Business Promotion. All rights reserved.