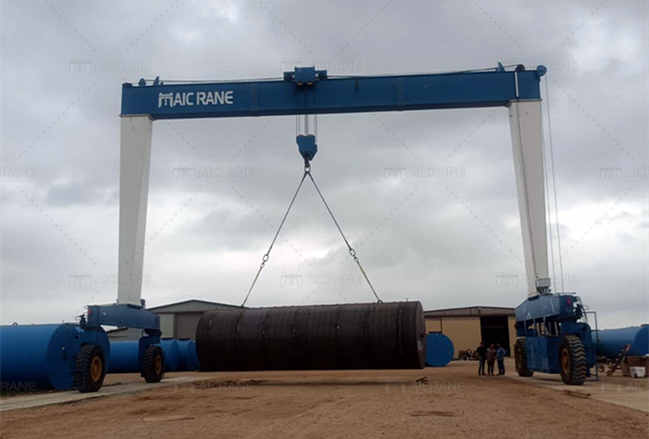
How to Influence RTG Crane Price
The RTG crane price can be influenced by several key factors, from specifications to market conditions.
© 2024 Crivva - Business Promotion. All rights reserved.