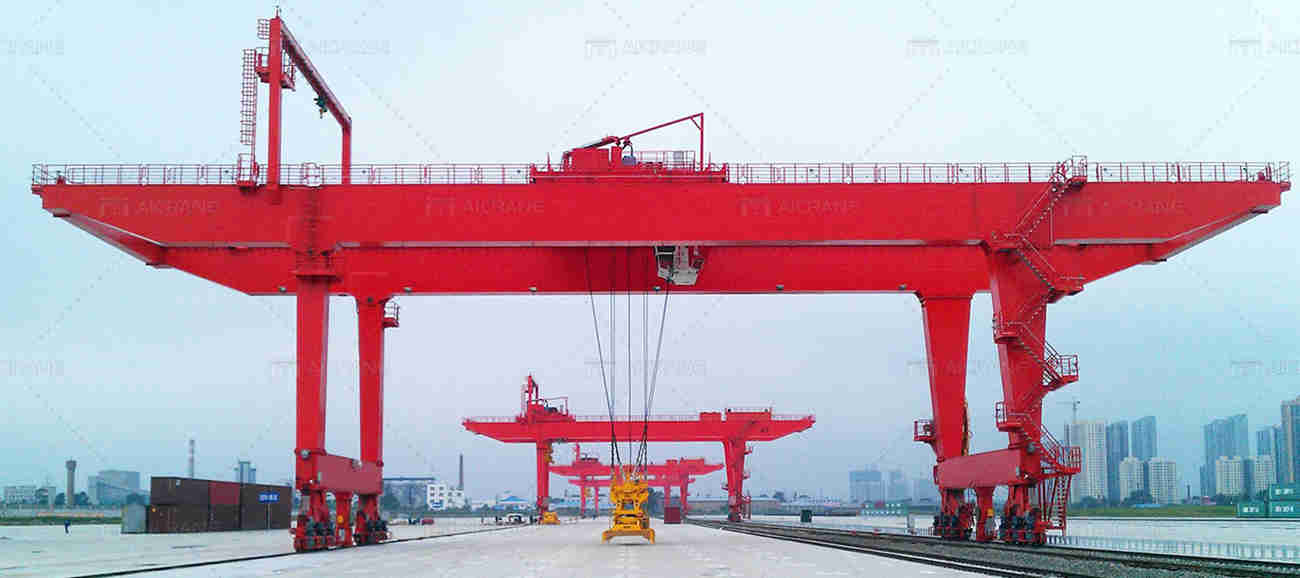
Tips for Maintenance for a 30 Ton Gantry Crane
Here are some key tips for creating an effective maintenance schedule for your 30 ton gantry crane.
© 2024 Crivva - Business Promotion. All rights reserved.